The seven new experiments have been selected after one month of detailed evaluation of project outlines that had been submitted for the second Open Call. The experiments include digital twin based solutions for the optimization of the beer mashing process, quality control and improvement of textile dyeing temperature control, quality control of glue application in parquet flooring manufacturing, improving the process of thermo-moulding for manufacturing of shoe insoles, predictive quality control for insulated glass machines, monitoring and control for reconfigurable presses to the improvement of continuous fiber additive manufacturing. The collaboration teams unite 19 new partners from Italy, Spain, Hungary and Turkey - among them 14 SMEs, 1 mid-cup, three research organisations and another Digital Innovation Hub external to the current network of DIGITbrain Consortium.
Get a detailed description of each experiment by clicking on the button right besides the respective experiment.
Experiment 15: Beerpredictor, a predictive tool for breweries to optimize the beer mashing process
While the adoption of “smart” brewing technologies has given a significant boost to the production effectiveness of the brewing industry, certain critical issues - most importantly, the complexities of the mashing process - still miss game-changing technological solutions. To date, the optimal mashing process – which sets some of the very essence of the style of the beer – has been determined by breweries manually, through producing trial brews and series of sampling, resulting in inefficiencies, greater costs, and incremental revenue loss. Our objective is to tackle this challenge by developing a digital simulation (our product, BeerPredictor), which supports setting and defining the correct mashing parameters, allowing small independent brewers to meet the specified carbohydrate composition of a particular beer style without intensive and costly manual tests – trial-and-error approaches - and analytical follow-up, based on the malt batch analytical parameters.
Beneficiaries of the BeerPredictor Experiment
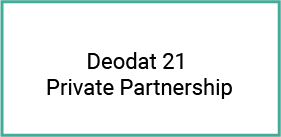
Deodat 21 Private Partnership
Innomine is the Digital Innovation Hub with the role of experiment supervisor.
Experiment 16: Anomaly Detection, Modeling and Adaptive Control of Textile Dyeing Temperature Control Phases (TEXAMAC)
Textile dyeing is the one of the main processes in textile sector. Textile dyeing process is a batch process and each factory has around 40 dyeing machines. The temperature control of the dye liquid in textile dyeing machine is a phase of textile dyeing process which takes about 70% of dyeing duration. Correct and optimal temperature control is inevitable for quality of desired color and decreasing color repairs which results in savings in steam, energy, water, chemical and dye usage. Our aim optimising temperature control of the machines by means of finding anomalies, creating digital twin of the temperature control phase and implemending adaptive control algorithms based on PI control.
Beneficiaries of the TEXAMAC Experiment
Innomine is the Digital Innovation Hub with the role of experiment supervisor.
Experiment 17: AI PARQUET QUALITY CONTROL (APRICOT)
APRICOT is an AI-enabled system for quality control of glue application in parquet flooring manufacturing at Bauwerk Group, leading parquet manufacturer in Europe from Switzerland. The experiment uses machine learning with Edge computing and NIR cameras to eliminate quality issues on an automated wood flooring production line in real-time.
Beneficiaries of the APRICOT Experiment
IMR is the Digital Innovation Hub with the role of experiment supervisor.
Experiment 18: Digital twin simulation of the shoe insole manufacturing process (INSOTWIN)
Insoletwin will create a digital twin of the process of thermo-moulding within the manufacturing of shoe insoles in the factory of Arneplant, the EU leader in shoe insole manufacturing. The project will be based on the existing solution of Digitaltwin Solutions. The Digital Twin solution will be based in the data, model and algorithm tuple proposed by DigitBrain with the aim to use the Digital Agora in their exploitation.
Beneficiaries of the INSOTWIN Experiment
ITAINNOVA is the Digital Innovation Hub with the role of experiment supervisor.
Experiment 19: Digital Twin and Predictive Quality Solution for Insulated Glass Machine (DTPQS4IG)
DTPQS4IG project aims to create a Predictive Quality tool with Digital Twin functions for Insulated Glass Machines. Insulated glasses are vital for sustainable building by reducing emissions. The emission reduction performance of the products is directly related to the gas filled in the insulated glasses. With that project, we make 100 % quality control of gas filling process by analyzing the IIoT data collected over machine controller and show the results to manufacturing operation over a digital twin.
Beneficiaries of DTPQS4IG Experiment
Simtera is the digital servization platform (fabmetrics) provider
DIGIT is the supporting DIHin the experiment
Experiment 20: monItoring and coNTrol for rEconfiGuRABLe prEsses (INTEGRABLE)
The experiment seeks to develop an experimental Data Driven Digital Twin which will permit i) edge in process control through a process stabilization monitoring and control system and ii) post process Quality Assessment combined with a continuous learning tool that will extract Geometry based Knowledge rules from multi machine XYZ Datasets allocated in the Digit Brain Platform; to "a priori" find improved Printing parameters and feed forward control strategies.
Beneficiaries of INTEGRABLE Experiment
START4.0 is the Digital Innovation Hub with the role of experiment supervisor.
Experiment 21: DIGITAL TWIN FOR CONTINUOUS FIBER ADDITIVE MANUFACTURING (DTCFAM)
A digital twin for the AFP process will be developed by advancing offline programming software. The solution will capture, and process data to identify defects in real-time alerting the operator to take the corrective action.
Beneficiaries of DTCFAM Experiment
IMR is the Digital Innovation Hub with the role of experiment supervisor.