Motivation of the Experiment
DITAC experiment will focus on the investigation and implementation of methodologies to introduce Digital Twin-based solutions to the design process at Restart Srl, an SME specialized in supply (from design to material realization) of tailor-made industrial automation solutions to provide important support in case of after-sales changes. In the Restart case, after-sales requests for changes from the final user are not isolated and they request significant work on the machine, causing interruption of work/production. The DITAC project aims to reduce the efforts needed for an after-sale change, providing virtual support/simulation for the required design changes.
The reasons beyond the usage of a Digital Twin can be listed as:
- Reducing commissioning interval: “testing” and commission is now performed at the customer's production site, also including travel costs for personnel who could carry out the activity in the office.
- Reducing system downtime regarding after-sales changes: as in the previous point, with the aggravating circumstance that the costs may involve production stops for the customer and / or activities outside the normal production activity (nights and weekends).
Optimizing the usage of resources, including also hardware and materials, avoiding the use of material erroneously estimated in the design phase. Furthermore, the aim of the project includes the design and testing of procedures and methodologies for faster development of digital twin, facilitated by a digital twin ecosystem. Moreover, the project will represent the opportunity for experimentation of data analysis through machine learning, supported (in case of lack of data) by “artificial” data eventually provided by the digital twin. For what concerns the ML sub-experiments part, following a phase of exploratory data analysis (EDA), a series of models will be trained to make predictions on the future state of the Restart Automation production line, also exploiting for the model training the data coming from the digital twin developed by IDM-Systems.
Purpose of the Experiment
The main goal of using digital twin-based technologies in Restart Srl is to reduce the efforts required for after-sale (on-site) modifications, with a significant improvement in service and a greater interest from new customers. The ultimate goal is to extend the company's range of action, through greater optimization of jobs that require a business trip for on-site modifications.
The main benefits provided by the introduction of a Digital Twin solution will be on the reduction of uncertainty in the case of changes after the realization and putting into production of the machine, improving:
- the amount of work “on-site” (fewer hours needed)
- the amount of machine downtime necessary (fewer hours needed)
- the overall quality of the process (less pressure during changes, since not performed “on-site”)
- find a non-trivial correlation between production phases regarding quality, providing earlier scrap detection (resource-saving) and better product quality.
From the perspective of software used, it will include both instruments for digital twin and machine learning development:
- Siemens Tecnomatix Process Simulate
- Siemens STEP7
- Siemens TIA Portal
- Siemens SIMIT
- Pytorch
- Fast.ai
- Pandas, scikit-learn and matplotplib
- Utilize in the cloud:
- Possibility to reach ML models onsite and separate ML model training
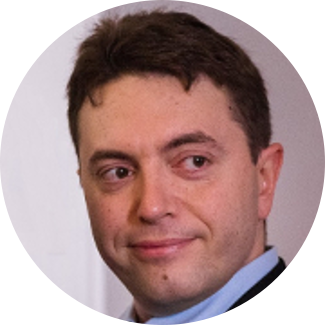
Andrea Ranieri,
Research Scientistat CNR-IMATI
"The machine learning classifier developed in the DIGITbrain project can optimize a production line by saving components. Even before a failure, parts begin to be marked as permanently lost, in real-time, due to the algorithm's predictions. I recommend participating in the project for SMEs interested in innovative technologies like ML and predictive maintenance."
Technical Impact
Regarding the development of digital twins, the main goal is to develop a stable, robust process and framework completing the current processes and using an existing, available market lead simulation software solutions (Siemens Tecnomatix Process Simulate) to create a fast, reliable and cost-efficient digital twin.
The target is to modularise IDM framework/method to provide a future-proof and easy-to-use solution for similar projects. The reason that these solutions are modularized and standardized makes the extension of the library easy. Therefore, creating another digital twin, even a different type of Industrial Product, is possible and the method for developing and integrating it into the framework will be already established.
Moreover, the consortium will also evaluate the analysis of data provided by the machine through a Machine Learning approach, including the use of Deep Learning (DL) models such as Convolutional Neural Networks (CNNs) or Long-Short Term Memory (LSTM) networks if classical ML models (e.g. Gradient Boosting methods) are not yielding satisfactory results. In this context, the main challenge is to analyse the data stream generated from both the real and the virtual machines.
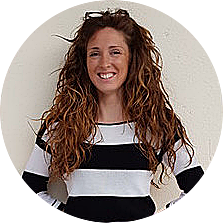
Margherita Costa
Marketing and Communication at Restart automation.
"The DIGITbrain DITAC project aimed to reduce the efforts, costs and downtime needed for an after-sale change, providing virtual support and simulation for the required design changes. In addition, our goal was to predict cable degradation in our production cell using the digital twin with machine learning algorithm."
Economic Impact of DITAC Experiment
All participants and the end-customers can benefit from the project, the main advantages of using digital twins and virtual commissioning are:
- Decrease of onsite needed time and of machine downtime benefit financially
- Shorter time for modification with less risk and cost at the end
- Less stress during the real commission thanks to the pre-tested PLC program
- FAT-test or pre-test are possible online with the end customer
- Better quality of the software and fewer warranty repairs required
- Digital twin modules extend the company's scope and improves the quality of service
- Offering of Digital Twin as-a-service and increases the interest of new customers (IDM-Systems has already received an order for a cell with multiple robots)
- Possibilities for predictive maintenance
- Reduction of downtime enables a reduction of lost income due to the limited production for the end-customer
- Savings in term of parts, which are marked as permanently lost due to the predictions
- Virtual commissioning can provide financial benefits for high-value single products as well

Tamás Jávor, Senior Project Engineerat IDM-Systems Zrt.
"The DIGITbrain DITAC project allowed us to develop a standardised virtual commissioning environment to pre-test PLC programs in safe environment. Further, it enabled us to extend our company’s scope in digital twin technologies and to offer digital twin as-a-service for new customers."
Watch DITAC's Experiment Video:
Project Partners
Restart Automation Srl.
is the experiment
end-user.
IDM-Systems Zrt.
serves as the
infrastructure provider.
CNR-IMATI
serves as the data model
& algorithms provider.
START4.0
is the Digital Innovation Hub
in this experiment.