Motivation of the Experiment
A costly and error-prone segment of the parquet manufacturing process is the manual quality control of the glue application process. Due to imperfections of wood, especially in production of large “rustic” parquet boards, glue is sometimes not uniformly applied, leaving gaps which later in the pressing part of the process cause pockets which are not glued. Once installed in a home, such boards can “pop-up” when fully settled and dried. Human error at this stage of manually detecting these gaps in glue application can result in many customer quality claims (hereinafter claims) which induce cost but also a lot of unneeded waste since packaging and shipping still causes environmental burden.
To cope with this problem this consortium wants to improve the quality control in the process and automate the process of quality checking and label any problematic plank for removal before the plank(s) enter the press, thus avoiding time spent working on malformed planks, reducing potential claims and reducing the CO2 footprint by avoiding any work on the malformed planks.
This consortium’s concept is to utilize high-end NIR (near-infrared) cameras, computer vision and deep learning implemented in the running system to detect glue application issues on the planks in real-time, on the edge.
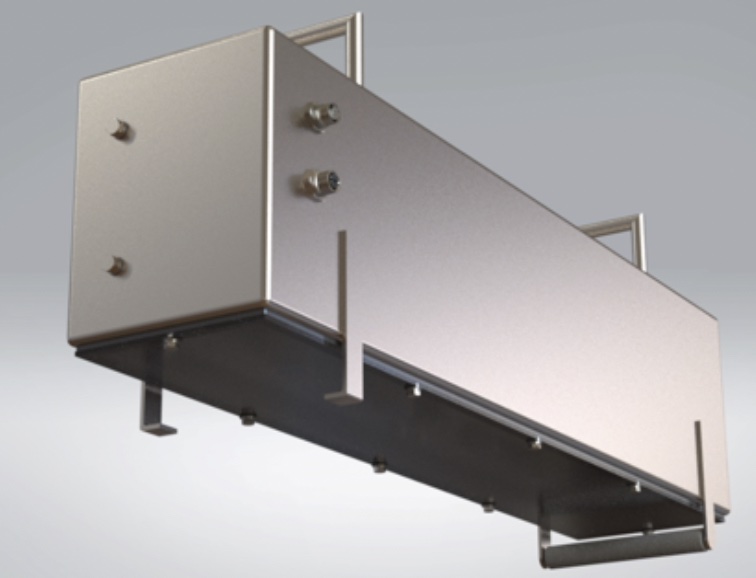
Plug And Play HW Solution
Purpose of the Experiment
The goal of experiment is to improve and automate glue application process quality inspection using cameras, computer vision and deep learning on the edge at end-user’s site. By doing so we will reduce costs, unneeded waste. The needed resources from the DIGITbrain Platform are the cloud (for data ingestion) and storage and the HPC for performing convolutional neural networks training on the ingested data. We would also like to use Digital Agora to sell partial solution and promote solution to other potential clients. With development of this solution, we will have a framework which can be applied to similar problems in the industry.
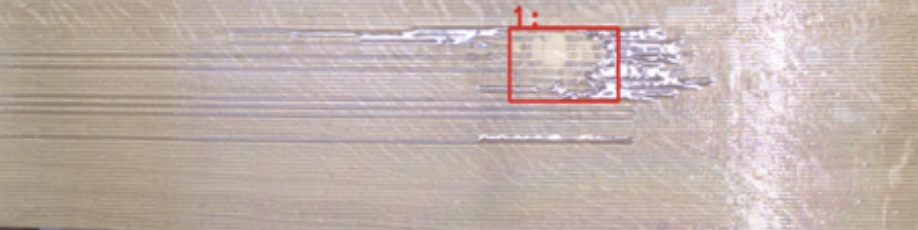
Plank No Glue Sample
Technical Impact
Bauwerk Group manufactures 11,6 million meters square of parquet flooring each year (estimate for 2022), out of which 80% is for the European market and 20% for Asia and USA, and it is the global leader in the quality / premium hardwood flooring segment.
By moving the 3 employees from the manual quality control of glue application process to a more value-adding position down the production stream to off-line repair, filling and touchup of finished products (parquet boards), BGHR estimates a gain of €215.000 per-annum in newly created value. The employees currently doing the quality control are female and by moving them to the filling and touchup position in the manufacturing chain they will be able to do a more rewarding job, with less fatigue and better compensation. By successfully implementing this solution in Croatian factory, BGHR hopes to roll out the solution to other 4 factories in Europe, scaling the benefits five-fold. This would mean the company can look to increase their manufacturing capacity by building more production lines and grow their market share.
Thanks to this experiment Ascalia will grow its portfolio of products and services catering to another high-value quality problem in manufacturing. It will also further increase scalability possibilities of the business using the same set of tools and software, ensuring long-term stability of the business model.
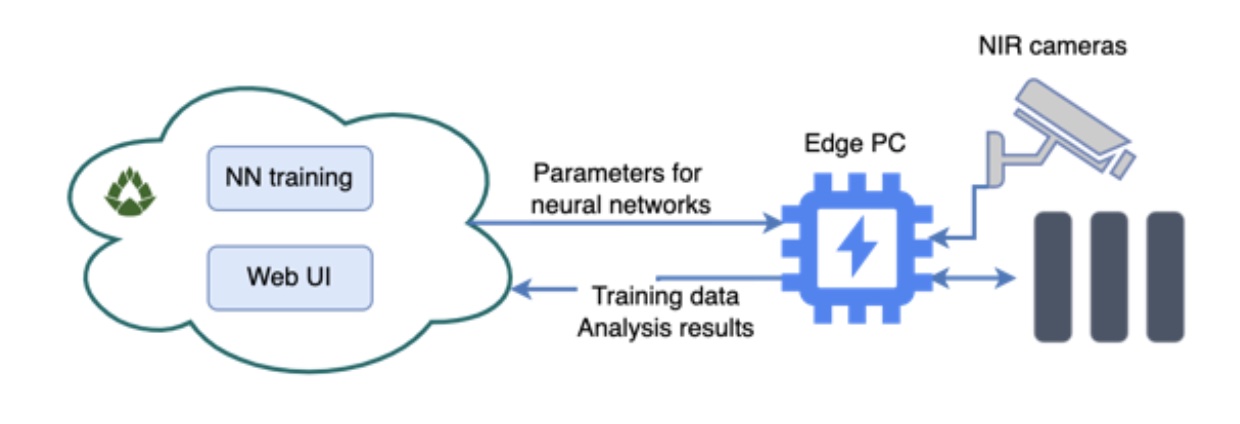
Edge AI Quality Inspection Solution
Expected Economic Impact
By moving the 3 employees from the manual quality control of glue application process to a more value-adding position down the production stream to off-line repair, filling and touchup of finished products (parquet boards), BGHR estimates a gain of €215.000 per-annum in newly created value.
Successful experiment outcome will also enable Ascalia to create at least 2 new job positions, one to further advance the algorithms and another to act as technical support to all the companies using the new product. Ascalia is currently mostly active in Croatia and UK with plans to enter the DACH region in the near future, an effort which would be sped-up with this product. In addition to scaling geographically, the product developed here can most probably be applied to adjacent industries – laminate manufacturing, solar panel manufacturing and polymer-based flooring, which will all be analysed in the business model analysis.
Project Partners:
Bauwerk Group Hrvatska d.o.o.
is the end-user
in this experiment
Ascalia d.o.o.
is the
Innomine
serves as the supporting DIH in this experiment