Motivation of the Experiment
Textile dyeing process is a batch process which takes 5-12 hours depending on various process parameters such as fibre of the fabric to be dyed, desired colour, chemicals and dye. A typical textile dyeing factory has around 40 dyeing machines with different dyeing capacities from 25kg-1200kg. Generally, all machines run simultaneously. The temperature of the liquid in the main tank is controlled by using PID (Proportional, Integral, Derivative) controller which takes about 70% of the duration of the dyeing process. To be able to obtain desired product characteristics, temperature of the dye liquid must track the reference temperature curves in a successful manner. However, this is not possible under current conditions, and therefore consumption and costs increase. Mayteks, one of the leading factories in this sector and based on these problems, they aim to digitalise and optimise its processes for environmental, quality and cost issues.
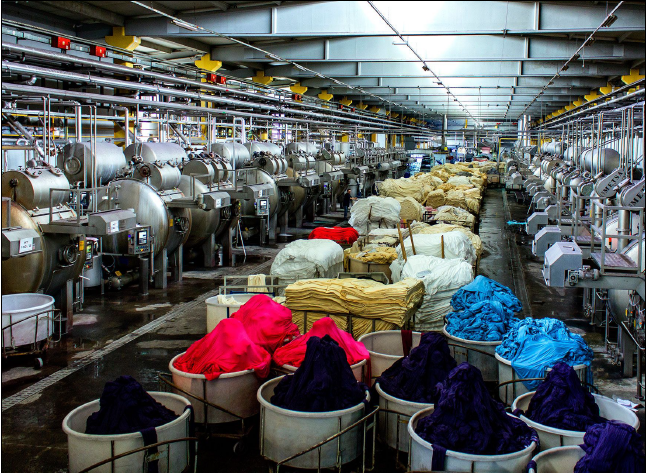
Textile Dye House
Within the scope of the experiment by creating a digital twin, temperature of the dye liquid will be simulated and optimization of the control algorithms such as anomaly detections and controller tunings will be realised more easily and efficiently. In the scope of this experiment to obtain a digital twin, 130°C Polyester fabrics dyeing process is selected in the textile factory. Polyester dyeing corresponds to 15% of all processes and it is the best sample for other fabric type processes. Estimated unit cost for the selected process due to temperature anomalies is 6.7€/kg. Production volume of Mayteks 103 tonnes/month and 8.7% batch redye ratio is required to solve current colour problems. This results in totally around €60,000 (103,000 x 0.087 x 6.7) extra cost per month for Mayteks.
Purpose of the Experiment
The temperature control of the dye liquid in textile dyeing machine is a phase of textile dyeing process which takes about 70% of dyeing duration. Correct and optimal temperature control is inevitable for quality of desired color and decreasing color repairs which results in savings in steam, energy, water, chemical and dye usage. In other words, to be able to obtain desired product characteristics, temperature of the dye liquid must track the reference temperature curves in a successful manner. Our aim in TEXAMAC experiment is optimising temperature control of the machines by means of finding anomalies, creating digital twin of the temperature control phase and implemending adaptive control algorithms based on PID control. In this context, edge resources for collecting and sending data to Docker micro-services which are running DIGITbrain cloud resources, and cloud resources for storing relational and time-series textile dyeing process data, digital twin models, smart temperature control and anomaly detection services are planned to be used in the experiment.
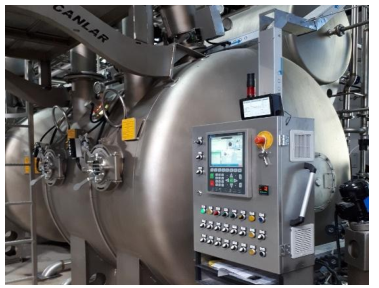
Dyeing Machine
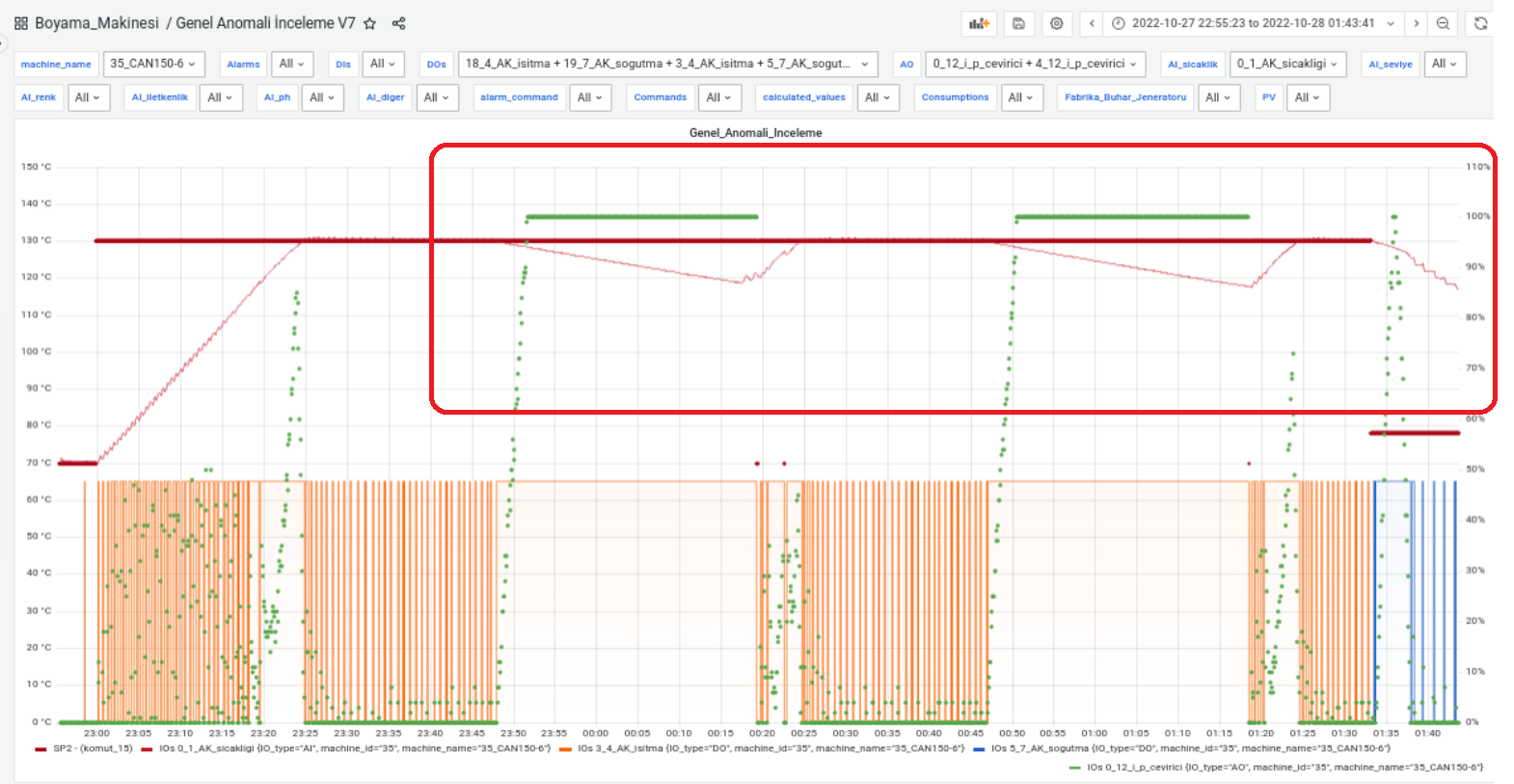
Heating Anomalies in the Dyeing Process
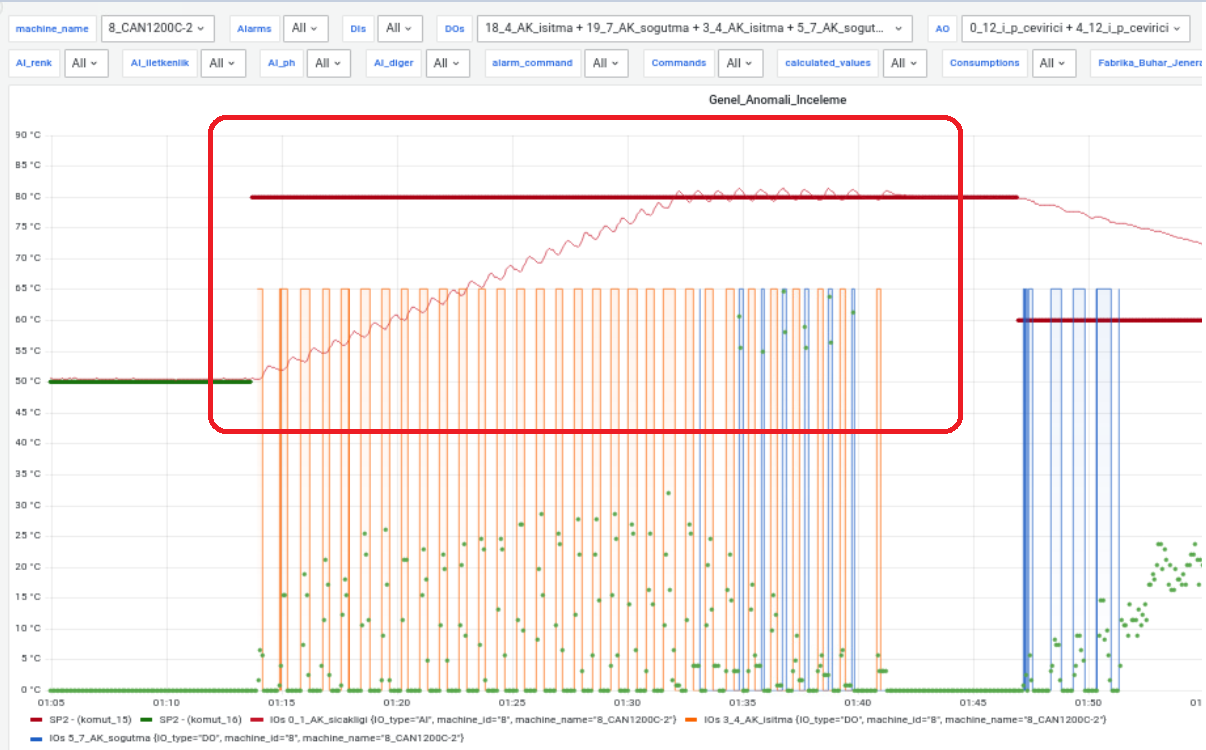
Oscillation Anomalies in the Dyeing Process
Technical Impact
Expected technical impact for the end-user (Mayteks);
- Process/tool/solution innovation: textile dyeing process temperature control anomaly detection and smart control. Adaptive to changing machine and factory conditions.
- Time reduction (engineering hours/engineering duration/production time/production): Average number of batches per machine in one day will be increased as process times are decreased. Right first time, technical support, preparing recipes, detecting anomalies faster.
- Process / product quality improvements: Production dyeing sample will be compared with the lab dyeing references with the base of ΔE (colour difference) value, the improvements will be regardable if less than or equal to 1 result in terms of client requirements is obtained. Percentages of oscillatory processes will be decreased from 2% to 0%. Average overshoot will be decreased from 3% to 1%. Average steady-state error will be decreased from 2% to 0.5%.
For the technical partner (Eliar);
- Software product innovation / improvement: Creating digital twin of temperature control in textile dyeing process, adaptive control, anomaly detection and adding value to current products.
- New distribution possibilities: Outcome of the project will be an add-on or special feature to the current product family. It is also possible to switch to a software rental model for Eliar products.
- Scalability / flexibility: Temperature control model may be implemented to Eliar mechatronics systems which weights, solves and distributes dyes to textile dyeing machines.
- New business models: MaaS will be a new business model for selling software which was designed and developed by Eliar. Besides the main purpose, project outcome is the first step towards a MaaS solution by moving our products to the DIGITbrain platform. Facilitating software installation and maintenance of software deployment processes
Expected Economic Impact
Expected economic impact of the experiment:
- Cost savings: Textile dye and chemical consumption will be decreased around 2,000€/month and around 15,000€/month for other expenses like steam, electricity, water, redye fabric stock cost, time etc. Totally around 17,000€/month.
- Job creation: One employee has already been hired for this project. Besides, to encourage women in manufacturing, an intern will start to work as the project has been kicked-off. In addition, new engineers may be hired to the R&D center of Eliar.
- Environmental: The textile process is a process that uses a lot of water, energy, chemicals and dyes. Therefore, the improvements to be made in these items will have a positive effect on the environment. After the supply of the digital counters, current and improved carbon emissions will be compared and environmental contributions of our project will be demonstrated.
- Customer satisfaction: Customer satisfaction will be increased as the average production delivery time shortens as a result of this project.
- Economical: For Eliar, software and maintenance processes are carried out in a shorter time. We will be able to rent the products we have developed.
Besides these outcomes, by using the cloud platform, it will get rid of IT support to the servers in the factory, get software updates instantly. In this way, it will be increased the success rate of dyeing processes both technically and economically, helping to get ready for the European Green Deal.