Motivation of the Experiment
While the adoption of “smart” brewing technologies has given a significant boost to the production effectiveness of the brewing industry, certain critical issues still miss game-changing technological solutions. Namely, the mashing process - the first crucial stage of beer production, essentially combining a mix of ground grains (mostly malted barley) with water, then heating the mixture – is driven by the degradation of the malt by certain enzymes, determining some of the very essence of the beer, i.e., its body, alcohol content, key flavour notes, foam, etc. The activity of these enzymes is mostly determined by the (1) temperature, (2) time as well as (3) pH value and (4) the mash concentration. However, all enzymes have “sweet spots” regarding these variables at which they break down in the most optimal fashion. Breweries must exactly know these critical figures to successfully determine the optimal parameters for their desired beer style. However, while statistical data may be available to help predict these variables, each mash has different characteristics. As such, the optimal mashing process is never the same, which has been traditionally addressed by producing trial brews and series of sampling, resulting in inefficiencies, greater costs, and incremental revenue loss.
Purpose of the Experiment
In the Experiment, the objective of our is to develop the prototype of BeerPredictor, which supports setting and leverage technology to reorganize the beer producing process, allowing small independent brewers - who do not hold large production batches and other industry-sized infrastructure – to reach the parameters of a particular beer style, eliminating the costly and inefficient test brewing procedures to successfully set these parameters. In short, our consortium’s goal is to determine if BeerPredictor’s prototype works at Karlwood.
When developing BeerPredictor, our technical team will rely on an open-source application, BreweryPi, which enables collecting and visualising different beer profiles. We plan to expand this tool by enabling it to process and store the mashing profile generated by our solution.
Technical Impact
As part of a large-scale technology revolution, digital investments in the beverage industry have exceeded USD 500 billion and continue to sharply rise in the sector – BeerPredictor, as a cutting edge solution will appear as a new technology that will help significantly build efficiencies, improving quality, etc. Although Beerpredictor will be a new market player, it will positioned as a high-tech, and reliable digital solution which is system-agnostic and offers seamless integration with various types of sensors and other hardware used in beer production management systems. Our consortium expects a rapid uptake of our solution’s market saturation in the SME brewery segment. What’s more, technology behind BeerPredictor may be adapted to any kind of FMCG manufacturing needs where the interplay between chemical processes of certain ingredients is crucial. The Experiment also allows for easy integration with the DIGITbrain Digital Agora that provides a standards-based ecosystem on which the Experiment and other, similar models can be deployed, executed, and exploited.
Expected Economic Impact
The Experiment will deliver several benefits for breweries. Firstly, it serves as a process innovation: BeerPredictor provides brewing expert personnel with the optimal mashing parameters in advance, reducing or even eliminating the need of the trial brews and the corrections in case the parameters of the trial brews are out of the tolerance range. Second, our tool will save costs and significant time. Most of smaller breweries are not equipped with sufficient labour resources and not even with in-line control equipment, therefore, BeerPredictor could save investments in a range of 5-10,000 Euros. (In running costs, a saving of appr. 1% extract can be realised due to lower loss and better yield.) BeerPredictor will allow to reduce the labour efforts of a process engineer by enabling them to avoid conducting intensive test brews – results of which may take days to analyse - and developing the necessary corrective actions.
Project Partners:
Karlwood Ltd
is the end-user
in this experiment
EN-CO Software Zrt.
is the software
provider
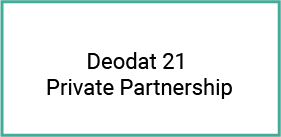
Deodat 21 Private Partnership
serves as engineering consultant
Innomine
serves as the supporting DIH in this experiment.