Motivation of the Experiment
The main objective of the experiment is to optimize the production of customized metal medical devices while considering the combined use of additive and subtractive manufacturing. This hybrid technique, often referred to as Sint & Mill (S&M), consists in creating a semi-finished product with a 3D printer and subsequently applying precision CNC milling for surface finishing. This process is known to reduce milling time up to 50% if compared to classical milling, greatly reducing material consumption, production time, and machine life-time. Despite being superior to classical manufacturing techniques, hybrid manufacturing still relies on suboptimal processing pipelines and, due to the high cost of the materials and equipment involved, it offers room for a further significant reduction of fabrication times and production costs.
The end-user PREMET operates in a Manufacturing-as-a-Service (MaaS) context, mainly producing personalized products designed by customers such as, e.g., dental technicians. At PREMET, the duration and cost of the manufacturing process depends on the size, orientation and number of the products on the build platform. These parameters have a high influence on the production cost of a given product. A product may cost from two to five times less if it is fabricated on the same platform together with other products, when compared to the cost it would have if produced alone on ist own building platform.
The problem is that the tasks before 3D printing are very time-consuming. By this we mean that 3D software does not respond or responds very slowly to certain parameters. Such parameters include the time of printing, the use of materials, the correct orientation, etc...In addition, they cannot take into account the quality of the resulting surfaces, the post-processing time and possible pricing. In addition, they cannot give recommendations on the correct orientation of the products on the platform.
The main ProMED objective is to optimize the production of customized medical devices Assisting the 3D printing operators to make informed decisions about the process. In metal 3D printing generally, several parts can be placed on a given platform that are produced together. In addition, the parts to be printed in case of medical devices are always different (even if they are within certain categories). The overall objective is to make production in an optimal way. However, optimums – at a given time, and for a given product or a set of products – can be completely different.
Optimum might be linked to
- priority to produce a given product (e.g. urgent order)
- time (shortest time of production for a given platform, or of a given
product) - cost (lowest cost)
- surface quality (e.g. the surface of a product has to reach a certain quality)
- mechanical properties (e.g. by using different process parameters)
- manual work (e.g. minimum manual post processing).
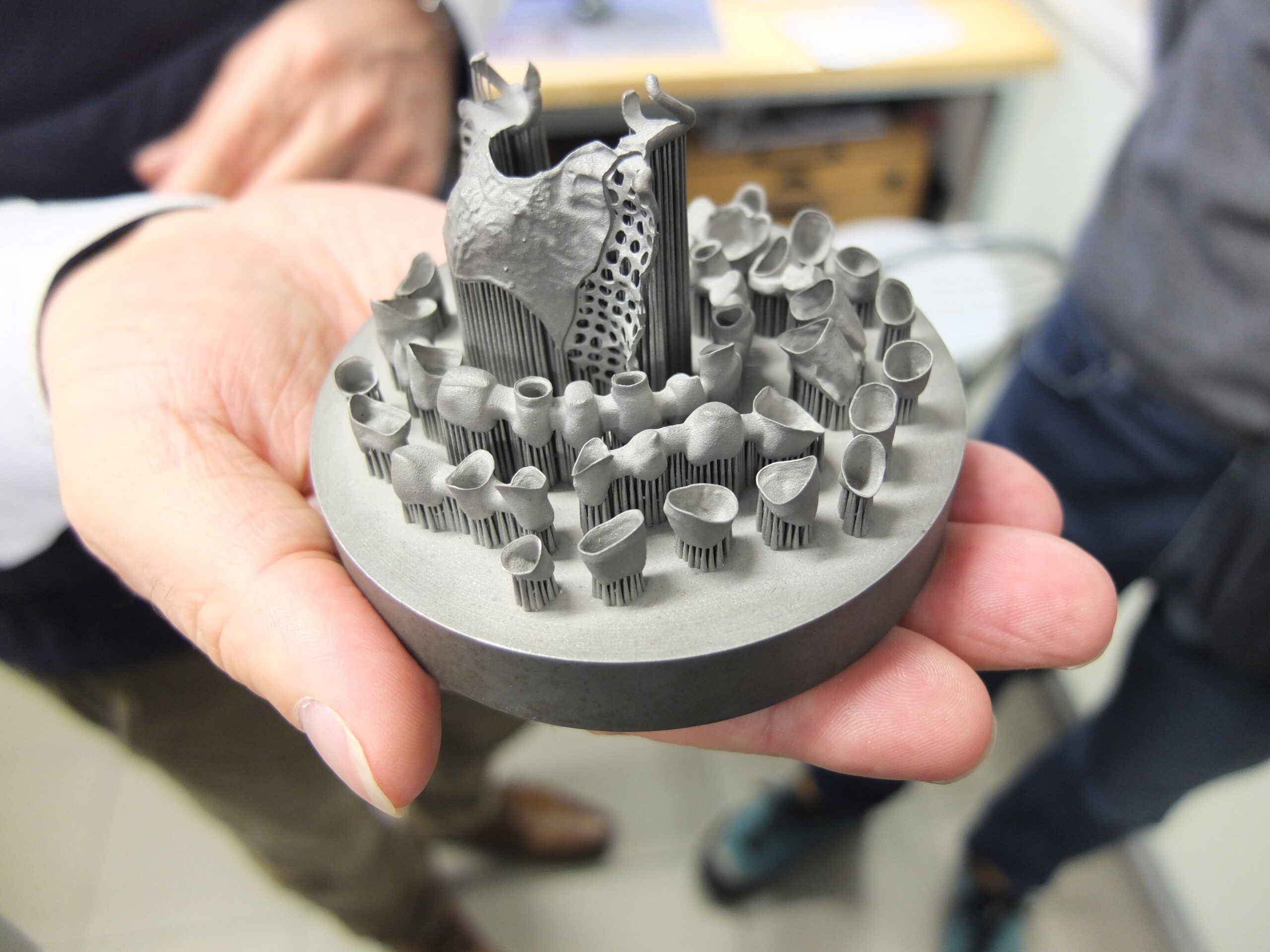
Purpose of the Experiment
Within ProMED, we plan (1) to support the end-user in the difficult task of formalizing the vague concept of "optimum" related to a Sint & Mill production, and (2) to develop a cloud-based decision support system which is able to simulate the behaviour of the production facility, predict how long it would take to perform a fabrication, support the end-user in the determination of the production costs, and calculate optimal parameter settings. The decision support system should help deciding how to best orient a part on the platform, based on parameters such as production time, surface quality, need for human labour, possibility to pack more products on the same building platform, etc. Ideally, the system should make the user aware of how the orientation correlates with the aforementioned parameters.
The system will take the form of a cloud-based service accessible through a standard web browser which provides a dedicated user interface.
What we would like to achieve by the end of the project is that the software that is being developed will help the manufacturing colleagues to start production with the most appropriate parameters. In addition, it should also provide the customer with more detailed information (for example, about the printing time or the price of the printed product).
Technical Impact
Products for implantology must be made of titanium, with high precision and smooth surface quality at given points and surfaces of the product. “Traditional” products are frames like crowns and bridges that at present are produced by molding and CNC milling; however, these are expensive and frequently face quality related problems.
Thanks to ProMED, production will benefit from an optimal parameter setting driven by the decision support system that we plan to deploy, so that the same products can be fabricated more efficiently, at a lower cost, and with a higher quality. Results of the experiment will be adaptable to any kind of AM enterprise, and not only for dental and medical ones. Algorithms and models can be incredibly useful,for any company looking to make 3D printing-based manufacturing economically viable.,The experiment allows testing geometric algorithms on the cloud, and makes it possible to assess their actual usability when integration with third-party commercial tools is required.
Thanks to ProMED, production will benefit from an optimal parameter setting driven by the decision support system that we plan to deploy, so that the same products can be fabricated more efficiently, at a lower cost, and with a higher quality. Results of the experiment will be adaptable to any kind of AM enterprise, and not only for dental and medical ones. Algorithms and models can be incredibly useful,for any company looking to make 3D printing-based manufacturing economically viable.,The experiment allows testing geometric algorithms on the cloud, and makes it possible to assess their actual usability when integration with third-party commercial tools is required.
Economic Impact
Using a traditional approach to fabricate dental implants leads to expensive products. Furthermore, these products frequently face quality related problems that represent an additional obstacle when trying to enter a market where competition is particularly tough.
According to the 2017 report of Wohlers the dental and medical sectors account for 11% of the whole 3D printing market. According to the estimation of Allied Market Research the market size of dental and medical 3D printing will reach 3692 million USD by 2026, with an average yearly increase of about 18.2% in the period 2019-2026.
The expected economic effects include a reduction in labour costs, as the software will allow workers to plan production more quickly. At the same time, it is also expected to increase revenues, as more production can be done in a day due to shorter lead times. Additive manufacturing is a waste-free manufacturing process by default, but there are limitations to the reuse of powder, but if more products can be added to a platform, the powder recycling cycle is reduced.
ProMed project Video
Project Partners
Premet
is the experiment end-user
in this experiment.
CNR-IMATI
serves as the data model
& algorithms provider.
OpenDot Srl.
serves as the interface provider
in this experiment.
Innomine
serves as the supporting DIH in this experiment