Motivation of the Experiment
Producer of manufacturing assembly lines faces unprecedented challenges in optimizing design and engineering to meet evolving market needs while ensuring, efficiency and productivity challenges.
- Providing a first-time right architecture, by balancing processes, sub-processes, buffers sizes;
- Providing the right mechanical solutions, by predicting critical problems before physical equipment testing to avoid wrong sizing/speed, force, torque/potential interferences, collisions or defect;
- Guaranteeing performances (rates, availability, quality) complying with customer’s requirements;
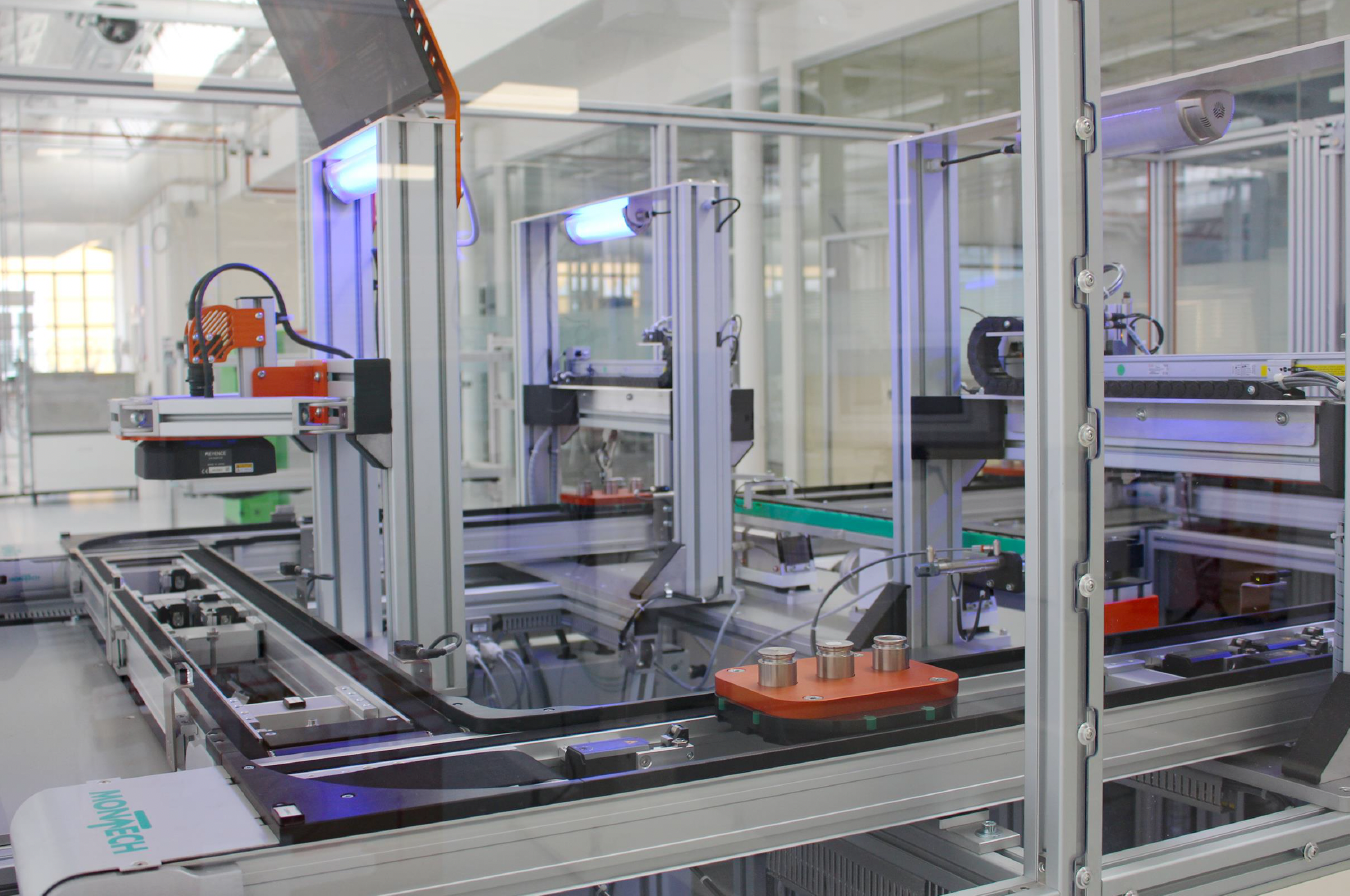
Pilot Assembly line at MADE - Test before invest
- Enabling the re-configuration of the machines to support different scenarios: new product variants, revamping, technology upgrading, by estimating the impact on the current design.
To solve these challenges, DIGITBreak aims at
- Developing, integrating and demonstrating a novel Simulation Based Digital Twin of a car brake assembly line production system leveraging EnginSoft, Cosberg and MADE competences
- Demonstrating advantages of such SBDT approach to new potential customers through the integration with DIGITBrain;
- Enhancing Cosberg ability to design customized solution allowing for improved cost efficiency; time consuming, time to market, quality and reliability;
- Developing a new MaaS business model, based on SBDT deployment on the Digital Agora
- Exploit DIH Test Before Invest scenario, facilitating end user market exploitation and replication
Purpose of the Experiment
The purpose of the experiment is to exploit digital twin to accomplish the following manufacturing scenario for the end-user:
Scenarios | Application fields | Key-Users | Drivers | KPI Target | Simulating Approaches |
1. Performance | Green field Brown field |
Designers Production Manager |
Architecture Bill of Material Technologies Process parameter |
#1 Throughput (Pieces/minute) |
Digital and Physical |
2. Downtime | Green field Brown field |
Designers Production Manager |
Technologies Process parameter |
#2 Availability (Running time/total time) |
Digital |
3. Quality | Green field Brown field |
Designers Production Manager |
Technologies Process parameter |
#3 Quality Index (Pieces OK /total pieces) |
Theoretical |
4. Revamping Technological Upgrade |
Brown field | Designers | Architecture Bill of Material Technologies Process parameter |
#4 OEE (Throughput, Availability, Quality) |
Digital |
5. Resource Optimisation |
Brown field | Production Manager |
Bill of Material Process parameter |
#5b Material (Bill of devices)To be monitored: #4 OEE |
Physical |
The project uses a Simulation Based Digital Twin (SBDT), based on Discrete Event Simulation models (DES) relying on engineering. knowledge and data to represent the behaviour of the plant. The underlying simulation model is used to obtain high-fidelity predictions, including production forecasts of new scenarios for which no past data are available. DES model requires limited computational resources: a full day of production of an assembly line with a complex production mix is simulated within seconds on a laptop. Exploiting the Test Before Invest the project will deploy different approaches:
- Digital and Physical: digital simulation of events and physical application by real testing on the pilot machine (scenario 1 – Productivity, scenario 5 – Revamping, scenario 4 – Resources Optimization);
- Only Digital: digital simulation of events, without any chance to test physically the solution (scenario 2 - Downtime);
- Theoretical evaluation: study the effects of simulating new events and haw could affect target KPIs (Scenario 3 - Quality).
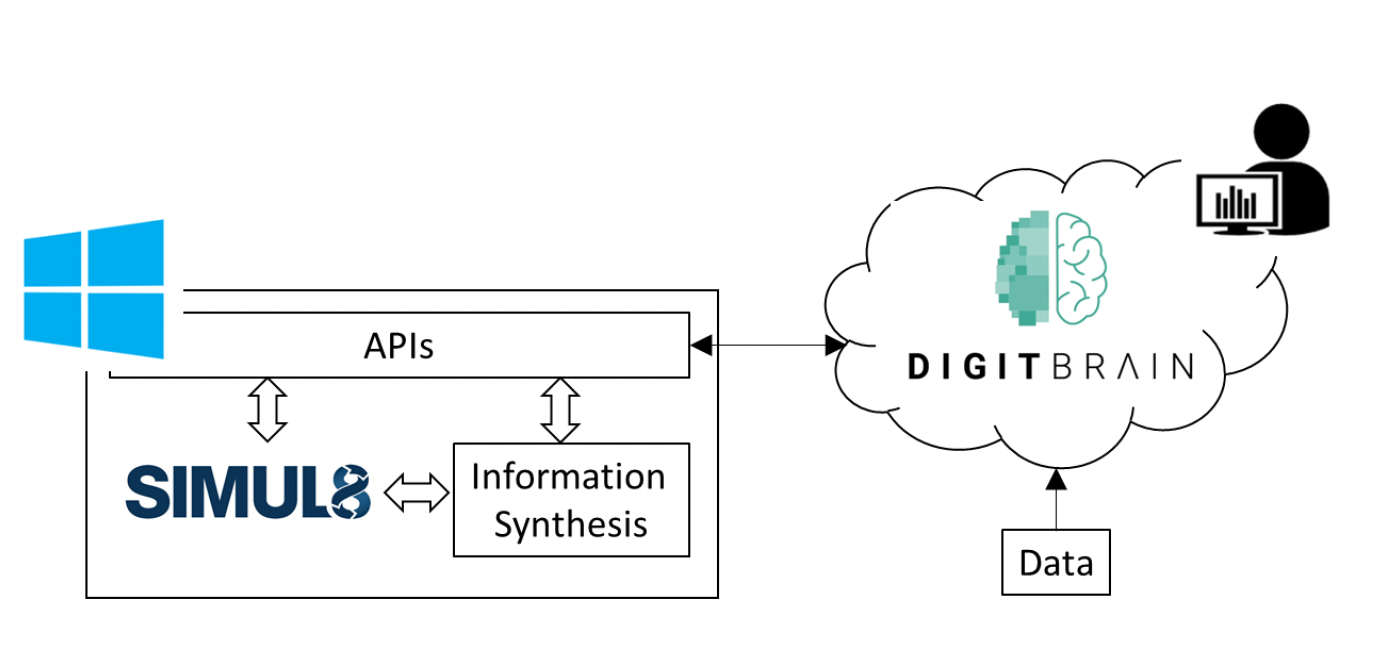
Discrete event simulation models of the assembly line
Technical Impact
The experiment follow Test Before Invest (TBI) methodology deploying use case installed at MADE Competence Center - Digital Innovation Hub. This scenario allow for simulation in real operational environment (TRL 7) minimizing technical and business risk of technology transfer to market both for end user and Individual Software Vendor.
The experiment builds on the following blocks: (i) pilot assembly line at MADE - TBI (ii) line monitoring system and data flow thereof, (iii) information synthesis layer, (iv) discrete event simulation models of the assembly line, (v) DIGITbrain framework, including the Digital Agora.
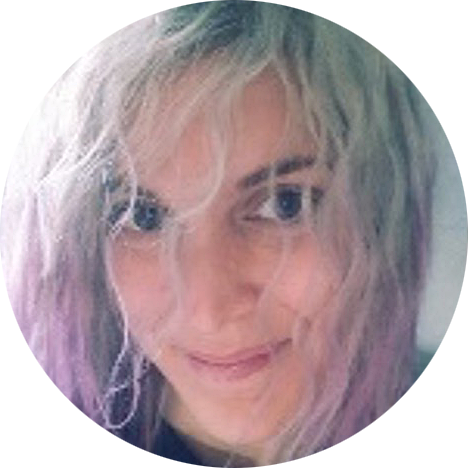
Project Manager at
MADE - Competence Center Industria 4.0.
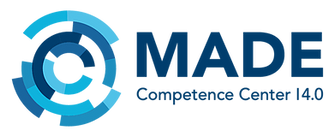
"DIGITbrain project allowed use to expand our Test Before Invest support services towards Digital Twin technologies and foster technology matchmaking in our ecosystem."
Economic Impact of DigiTBreak Experiment
The DIGITBRAKE project released
6 digital model on specific manufacturing scenarios formalized to develop and test the feasibility of solutions: improving performance; reducing downtime; increasing the quality of the processed product; revamping plant with technology overhaul; and optimizing plant resources, with the same performance;
1 interface, supporting manufacturing operators and manager to deploy
1 app integrated into the DIGITBrain platform
+ 4 new employee focused on digital manufacturing skills
+ 3 business model innovated, for end user, technical provider, DIH
+ 5 new contacts for business and R&D opportunities
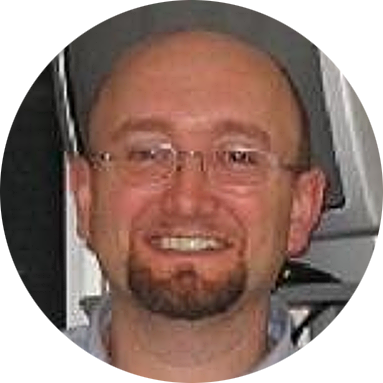
Giovanni Borzi,
Business Unit Manager Industry 4.0 at EnginSoft.

"DIGITbrain project was a great opportunity to explore Manufacturing As Service Business model with new end user, generate and integrate innovative digital models for a more productive, cost efficient and resilient manufacturing processes."
Watch DigiTBreak's Experiment Video:
Watch DigiTBreak presentation at Hannover Fair 2021:
Project Partners:
Cosberg S.P.A, Italy
serves as the end-user in this experiment.
EnginSoft SpA., Italy
serves as the technology partner.
MADE s.c.a r.l., Italy
serves as DIH in this experiment.
START4.0 is the Digital Innovation Hub with the role of experiment supervisor.